Machining the main landing wheels
Wednesday, 29th August, 2018
Forgive me if my diary keeping has become erratic in its chronology: In my most recent posts I’ve been describing work in July and August, while for this latest episode I revert back to May! No matter. Better late than never.
Machining the main landing wheels of a 1:5 scale Spitfire model out of solid 2.5-in diameter machine-grade aluminium bar is not a job to be approached lightly, and not least because significant planning is involved, principally in how to simplify the internal structure such that a home machinist operation becomes practicable, while at the same time preserving a semblance of realism for those determined to peer in between the spokes.
Paul Montforton’s drawing include excellent renderings of the three-, four- and five-spoke wheels, and I chose the middle option for my Mk IX. The overriding starting criteria were that each wheel would have to be made in two halves and bolt together so as to enclose and ‘pinch’ the tyres and that the out-of-scale bolts would have to be hidden. The external surfaces, front and back, would be as true to the original as possible; internally, significant compromises would be made… and this is where the planning comes in.
In many respects what I describe here bears a close approximation to the comparable manufacture of the spoked wheels for my 1:5 scale P-51D Mustang, which I describe in my ‘P-51 Diary’
http://www.spitfireinmyworkshop.net/story.php?id=18&title=machining-the-wheels
For that reason alone I’ll avoid going into great detail here, and let my pictures and captions do the talking…
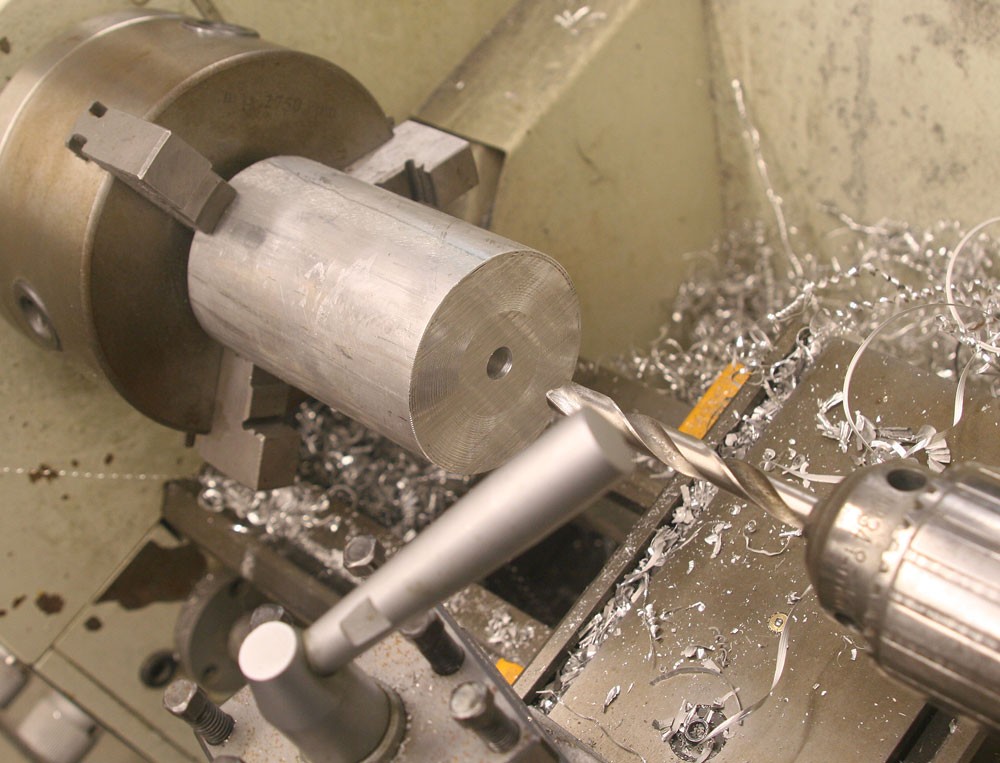
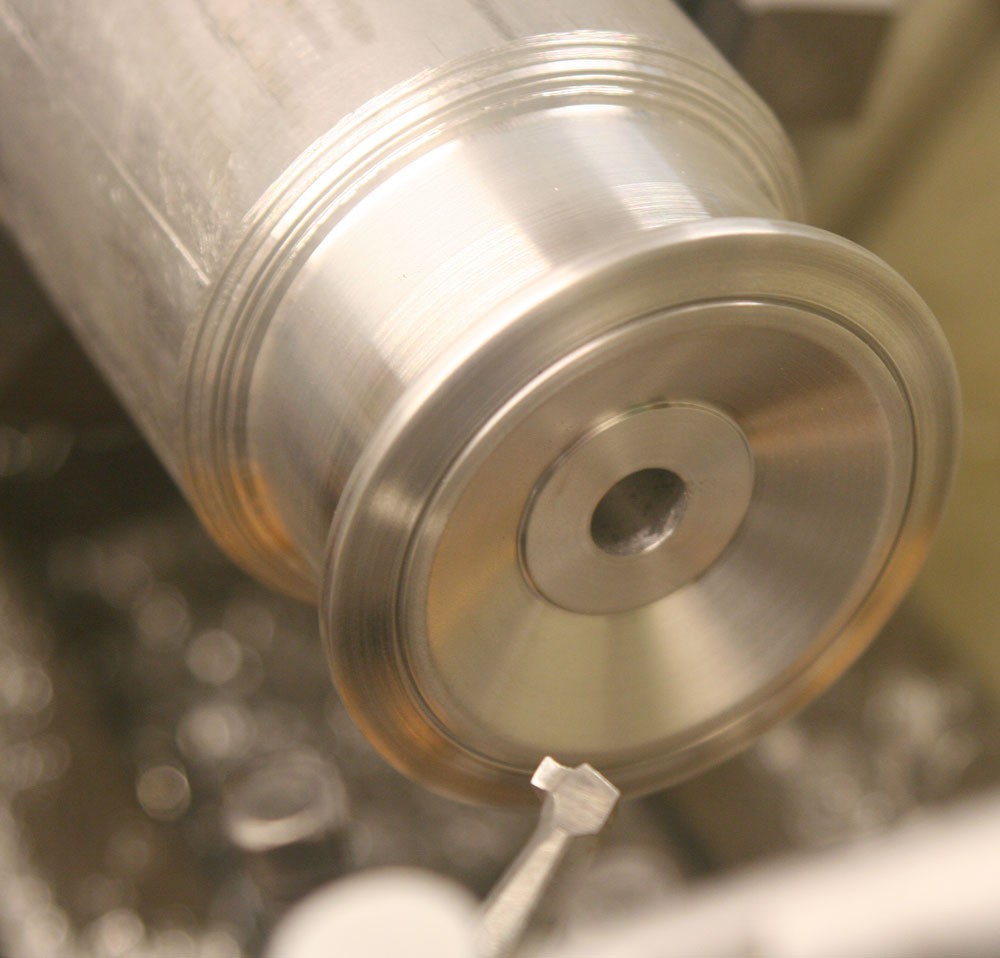
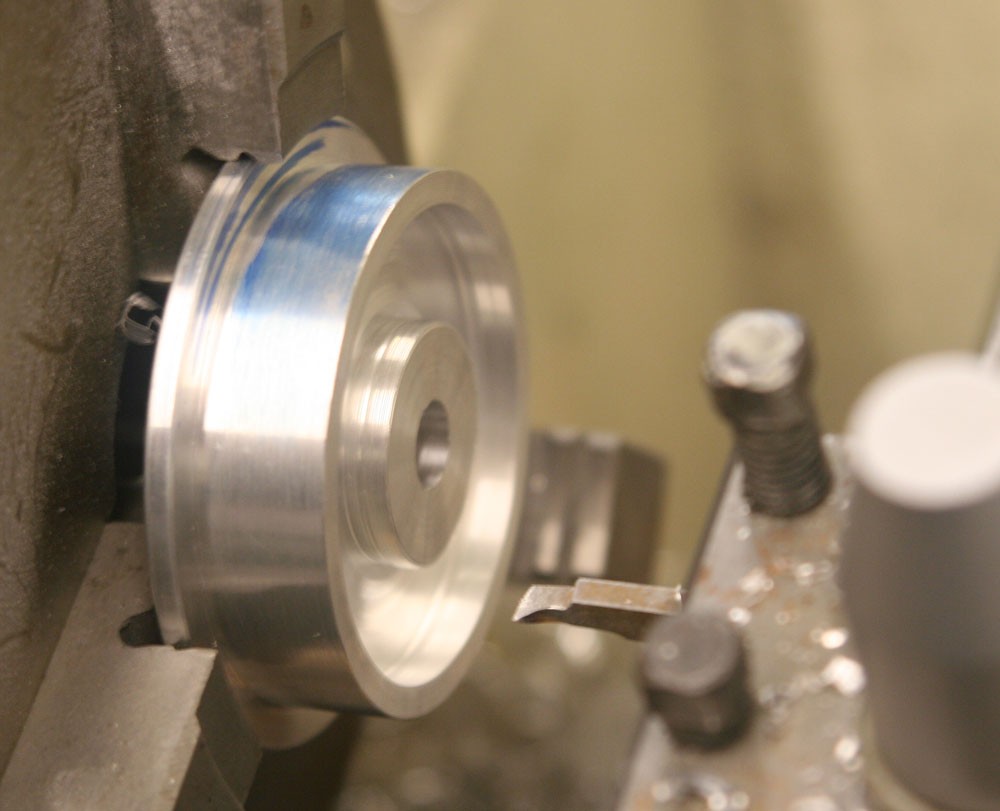
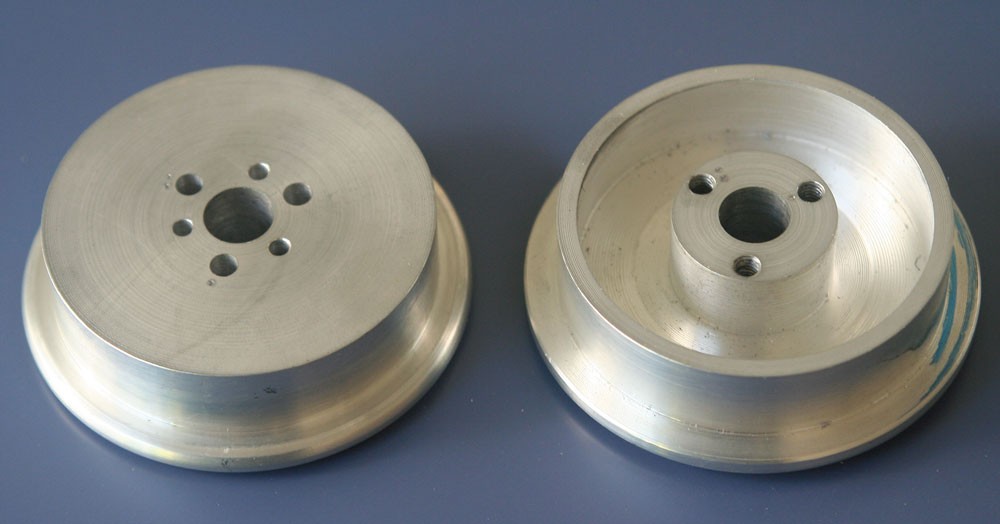
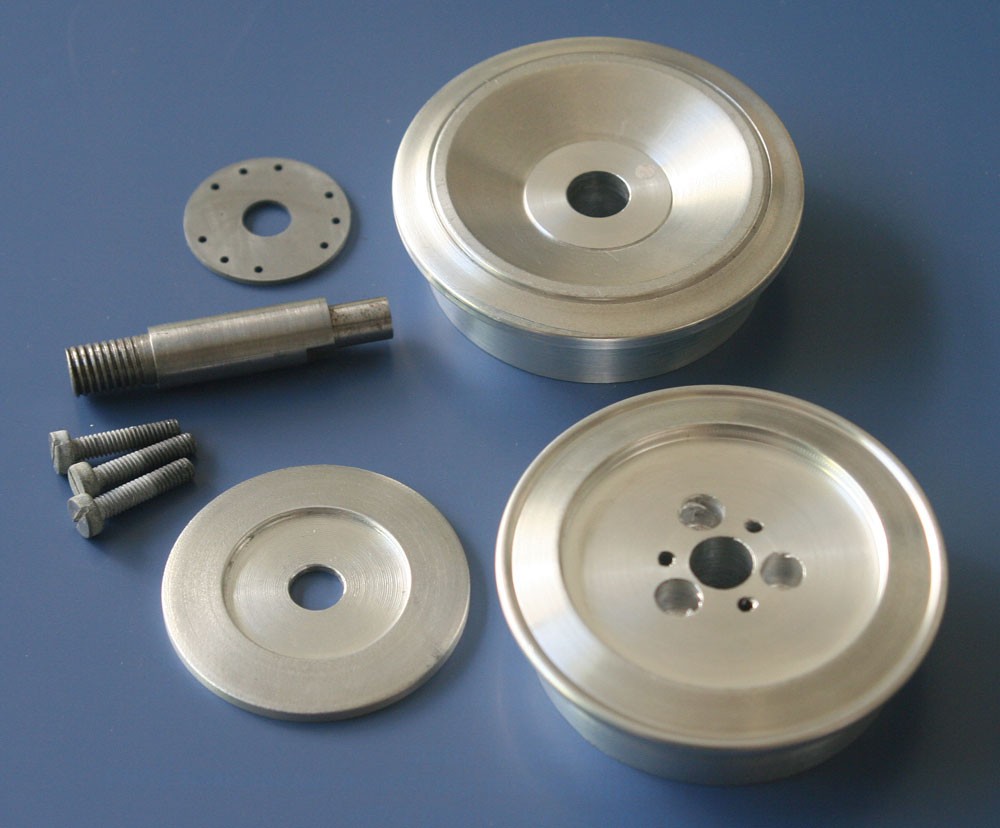
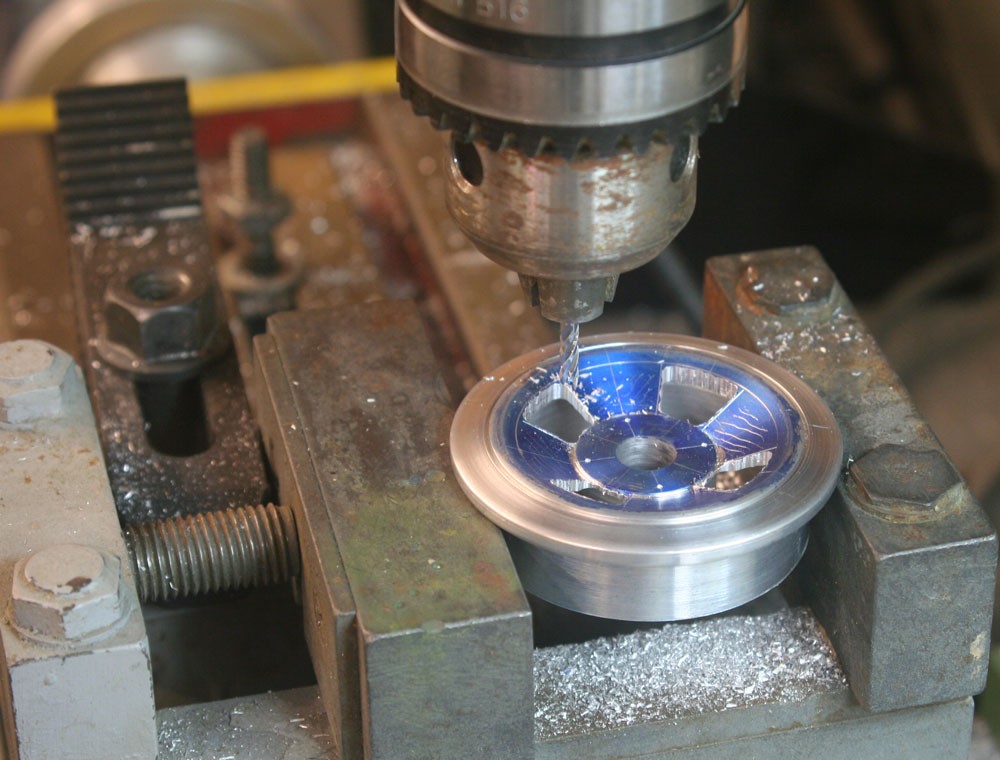
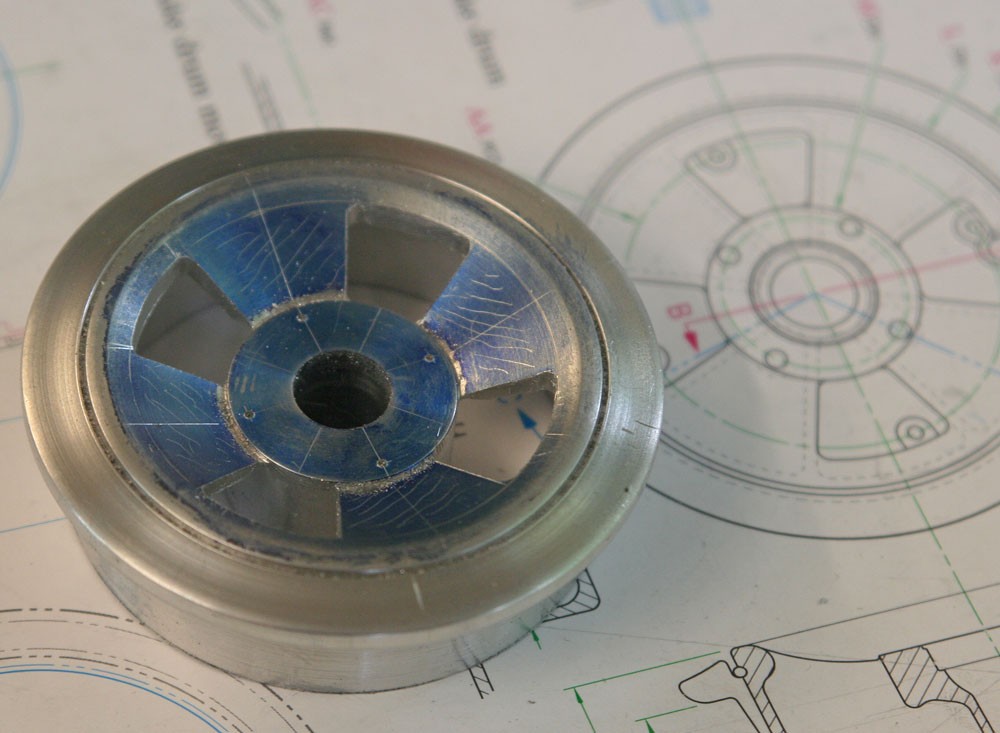
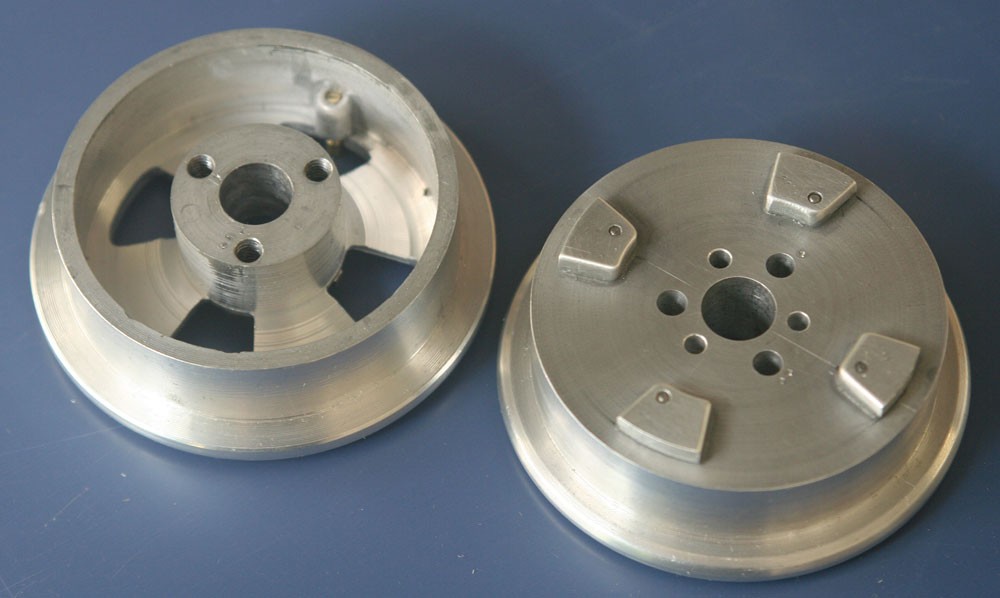
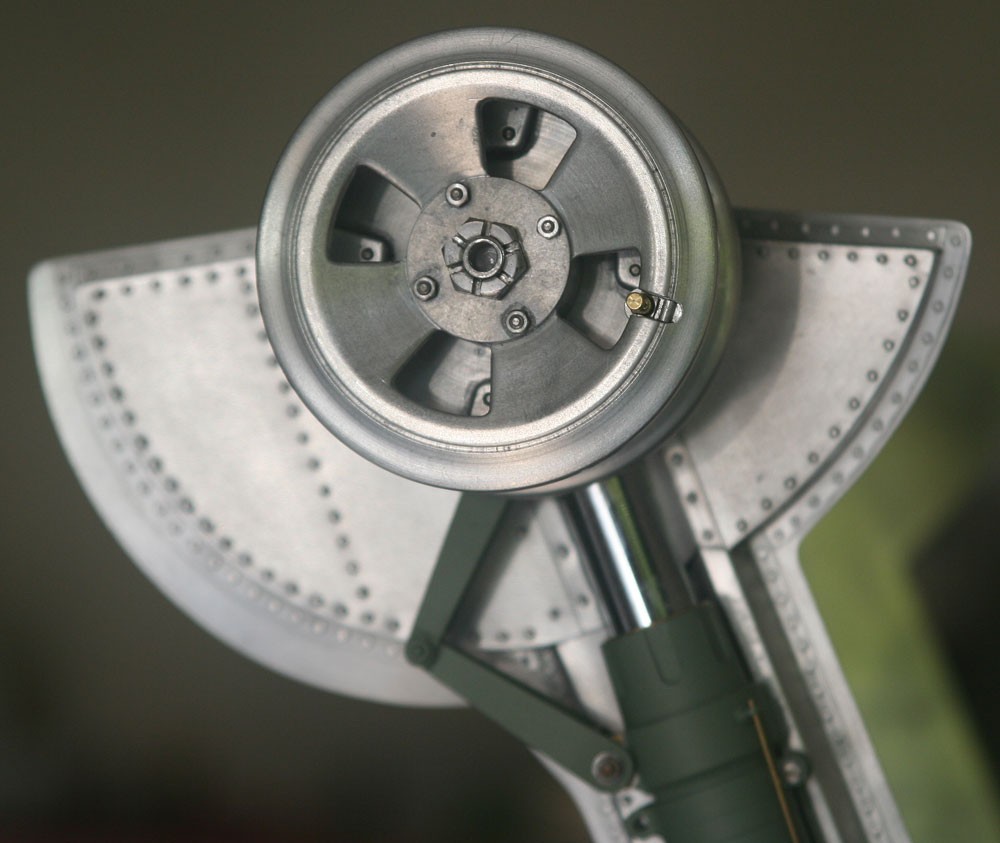