Oleo strut - Part 3
Monday, 18th May, 2015
Reductionism is a term frequently applied to science. It means describing a complex phenomenon in terms of its simple or fundamental constituent parts. Making the scissor bars for the oleo struts is not science, but their shape does present a potentially daunting challenge – until you start to look at them with a reductionist’s eye.
The first step is to isolate in the mind’s eye the main features of the geometry, which means mentally excluding all the curves: Now the interior web of the casting emerges as a simple triangle with two holes in it; sandwich this between a pair of cube-like shapes at either end and you have the three-dimensional makings of the attachment lugs and knuckle; flank the entire wedge with two flat sides and the basic form is in place.
I made the piece entirely of brass since it will be painted later, and the photographs show the sequence up to this stage, beginning with the silver soldering of the four end pieces to the web (Photo 2). With the waste material cut away and the flanks milled flat, the thin sidewalls are soft soldered in place at a lower temperature (so that the former work does not melt) and then milled flush top and bottom (Photo 3).
Now the shape can be finessed, beginning by milling the required slots and flats at either end of the piece (Photos 4 and 5), followed by drilling both ends for their connecting pins and bolts. This opens the way to rounding off the lugs, which I did by hand – but to make a neat job I turned two short cylindrical mild steel guides, one for either end, as an aid to the filing (Photo 6).
Obviously, the process I describe here must be repeated so as to create two pairs of two scissor bars, which differ from each other only at the knuckle end, but the reward for a lot of hard work came at the test fitting stage when – with no more than minor adjustments – all four parts could be bolted to their oleos.
One task remained – to reinstate the soft, rounded finish that is so characteristic of the un-machined parts of a casting, including those internal curves that were mentally purged at the start of the process. To do this I packed all four corners on both sides of the web with plastic metal. Then with the job set up horizontally in the milling vice, and with an appropriately sized end cutter in the chuck, I cut the internal radii. The solder had already started to fill and round off the joints length-wise and breadth-wise, but to accentuate this I added a few drops of very thin cyanoacrylate glue and let it flow around inside the piece. Repeated once or twice this had just the desired effect (Photo 7).
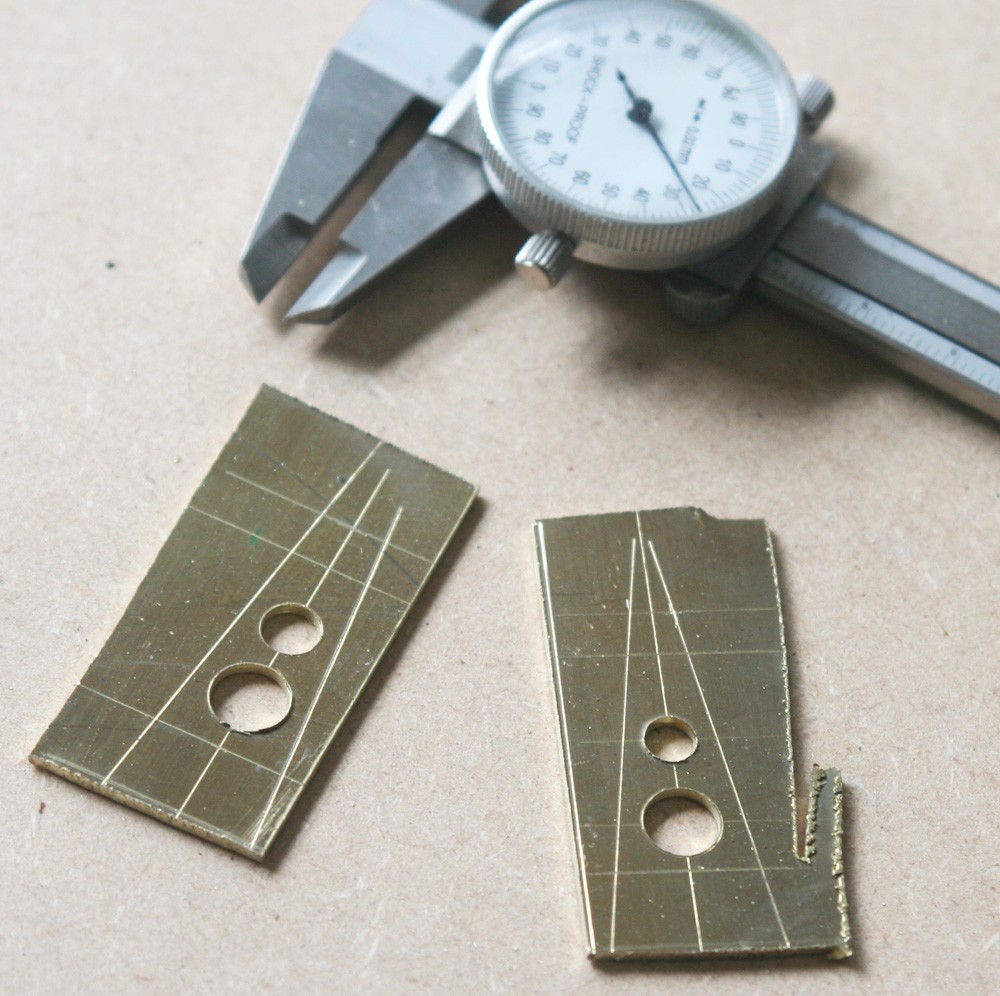
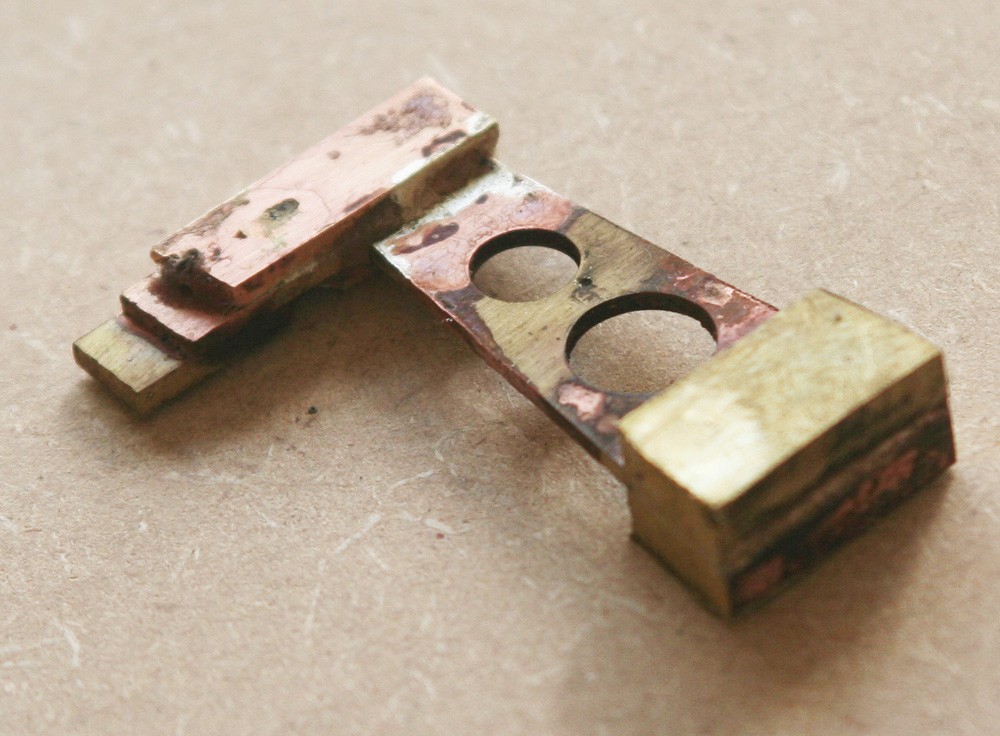
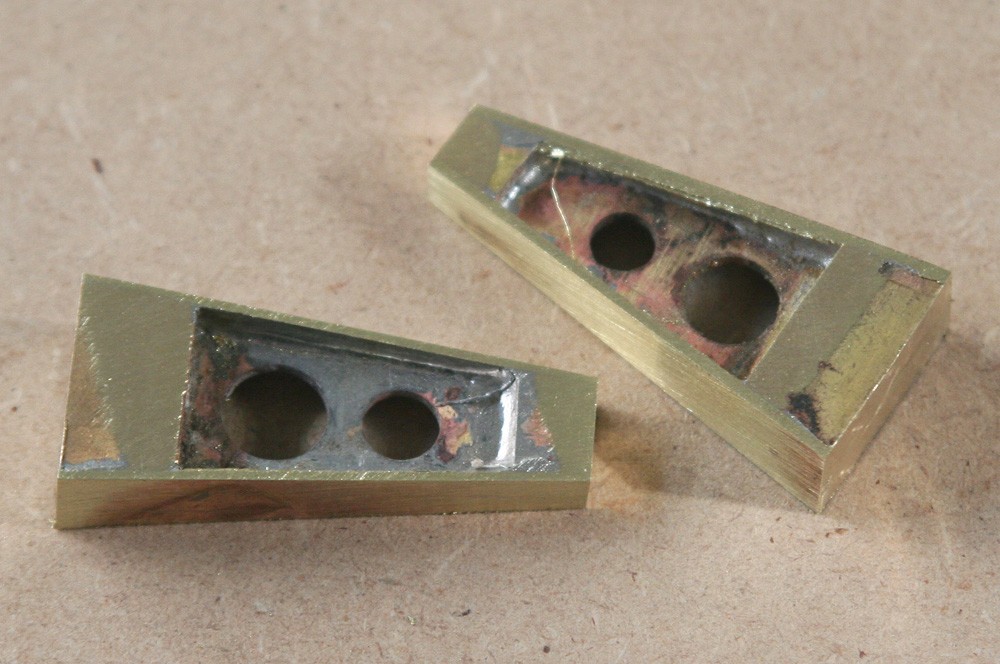
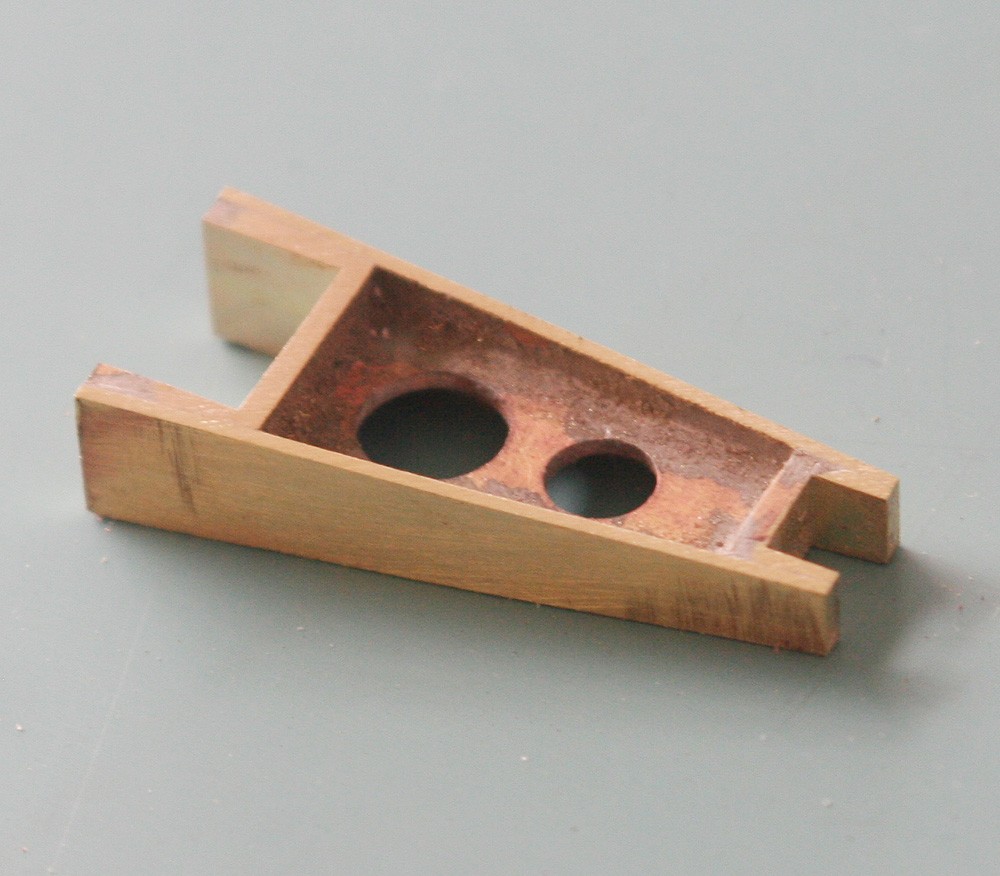
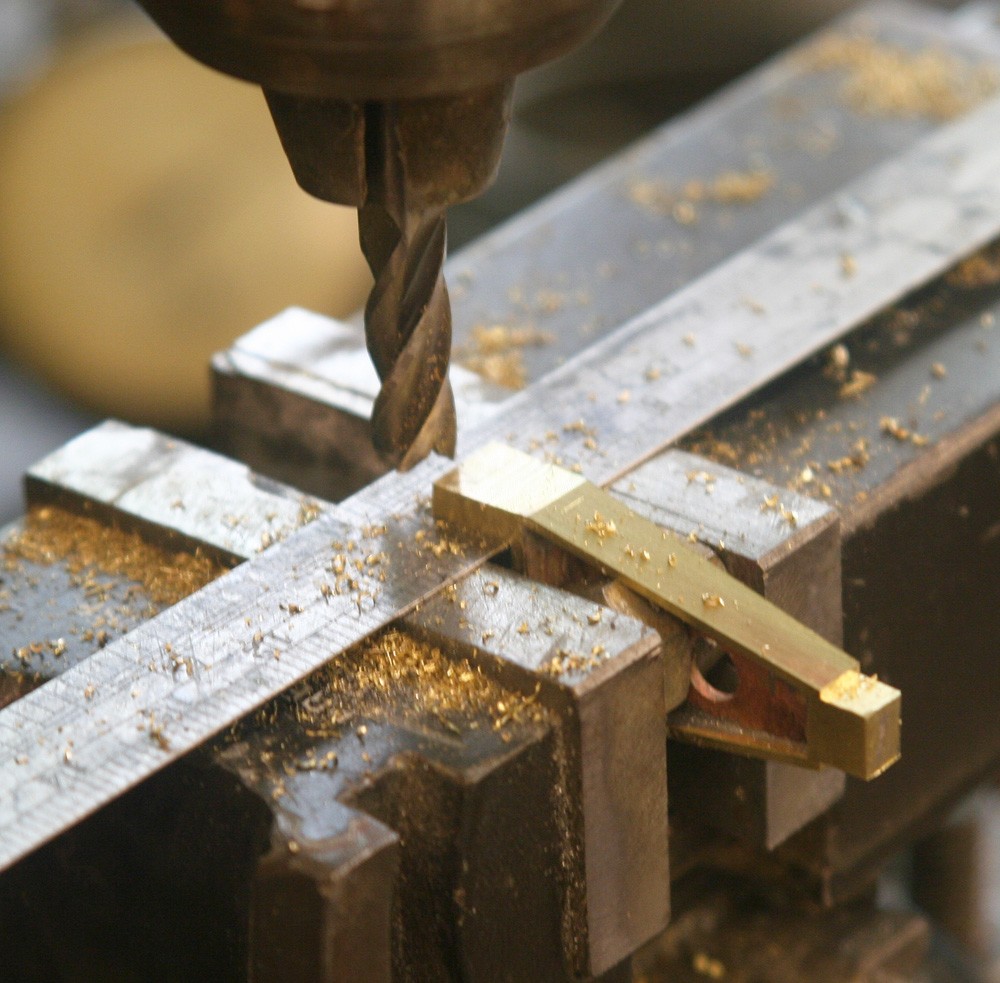
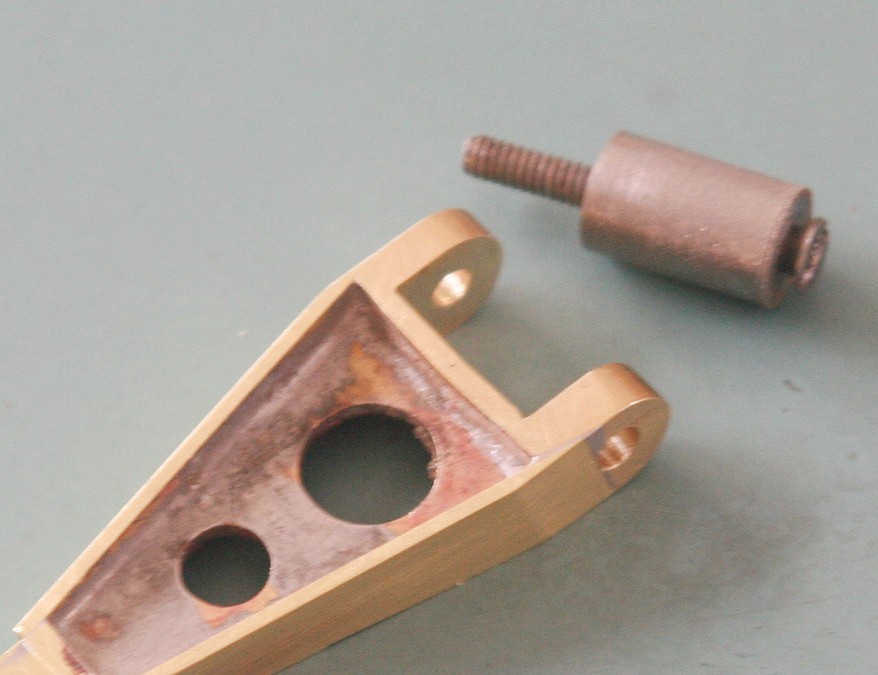
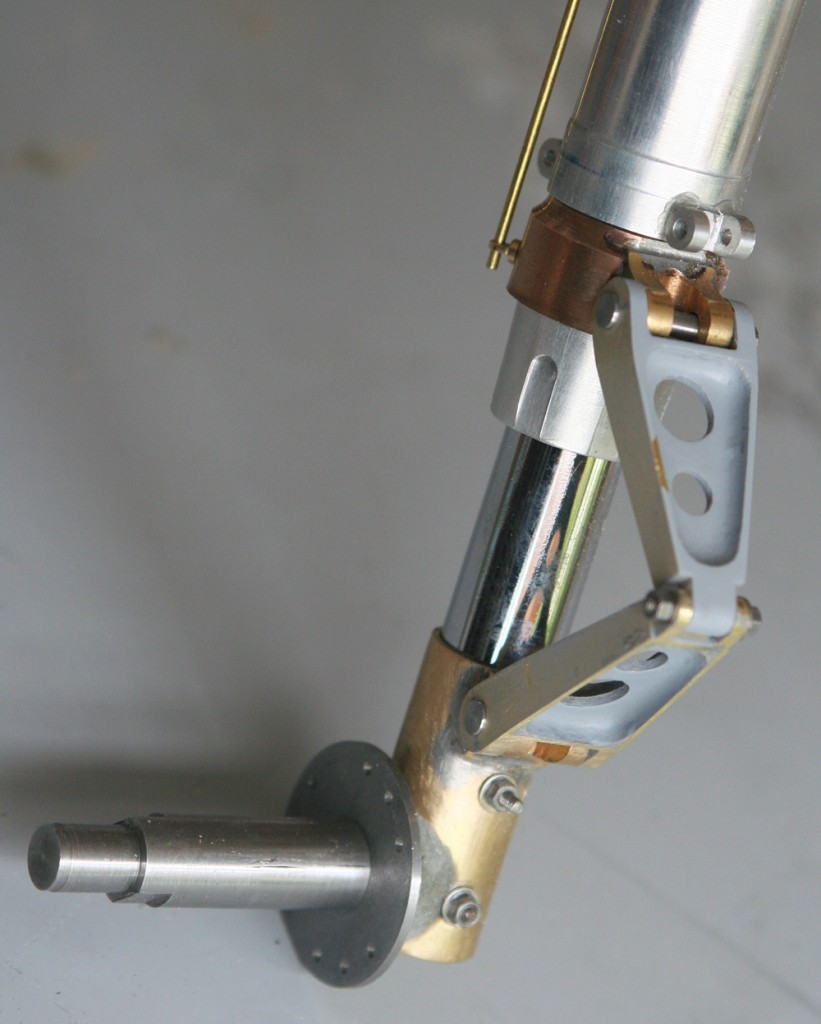